Professor: Andrew Witt
Course: Structural Surfaces
Contrary to how traditional joints have commonly been used for the construction of structural surfaces and spatial structures, this project’s goal was the research of a system to manufacture a set of standardized joints, with the use of multi-material 3d-printing, casting, and other fabrication methods.
By using finite element analysis to program different behaviors, we were capable of simulating and program different behaviors inherent to each of the joints in our catalogue — with the purpose of mimicking the way mechanical joints would be have to allow or restrict for rotation and displacement. Some of the joints, for instance, behave as a ball joint (allowing for rotation in the x, y, and z axes) while others behave as a mechanical hinge (allowing only for one-axis rotation).
Over the development of the project, we tried two different approaches to modify the behavior of different joints.
1- f ( Volume, Joints ) = Behavior
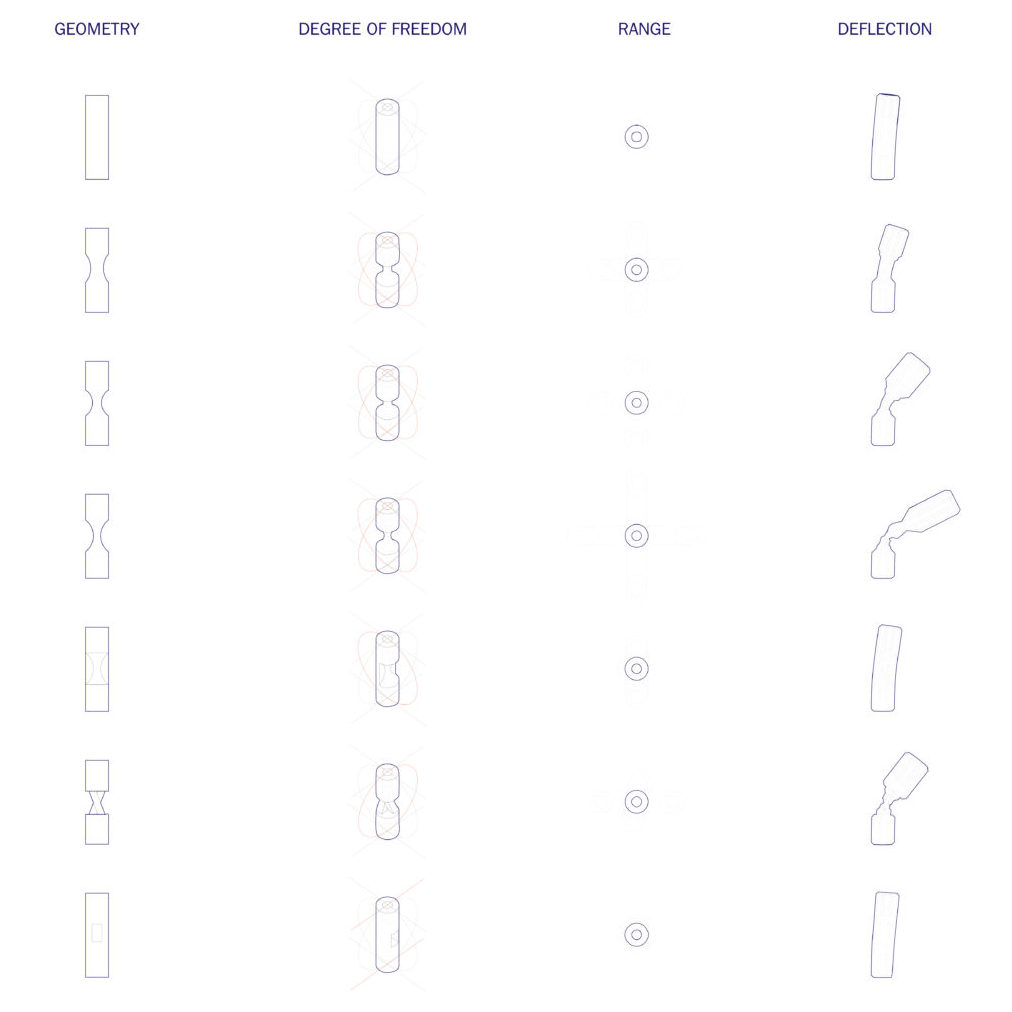
In the first approach, we used joints of similar geometry with different material distribution. (This is, different concentrations of flexible and rigid material, to have some areas that allow for deflection, while others would be completely fixed.) In the second approach, we used a single material and varied the geometry of the joints slightly to make them behave different. (This way, some joints would allow for more rotation or displacement than others because of their proportions in relation to the others.)
Harvard GSD | Spring 2016 | Group of 2